Specialty Rigging
NCSG offers customized specialty rigging services to customers and projects across Western Canada.
NCSG can provide our customers with a full complement of rigging of various sizes including spreader bars, shackles, slings, wire ropes, man and material baskets, turnbuckles, grommets, etc. We can also provide wooden crane mats and swamp mats upon request.
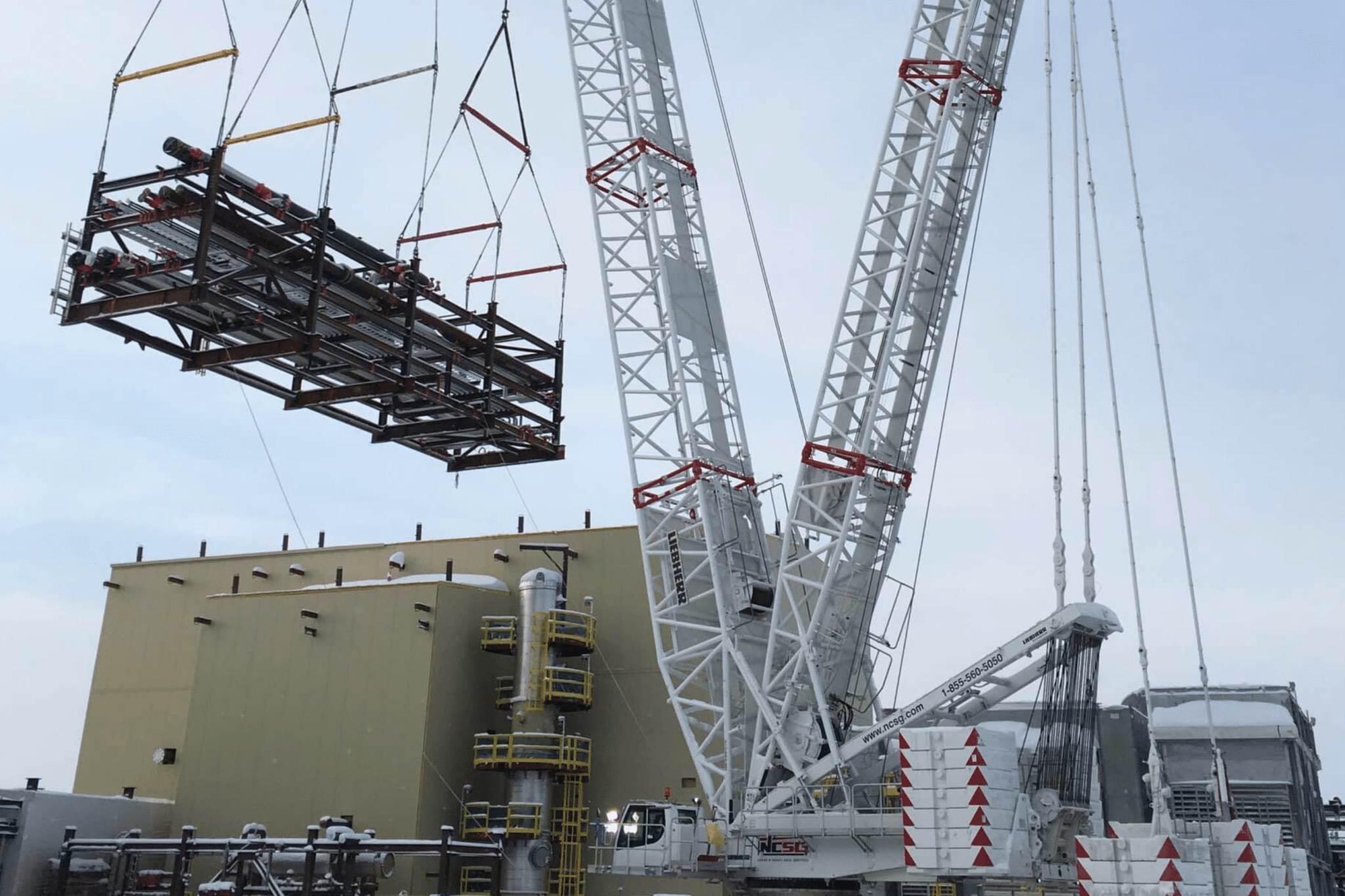
QuikMod Spreader Frame
NCSG Engineers have designed, certified and patented a specialized “QUIKMOD” spreader frame to lift modules (i.e. piperack, cable tray, equipment, coldbox) and process skids up to 175 tons.
This frame configuration can be used to lift modules with 4 to 12 pick points. The maximum module length it can handle is 150’ and the maximum weight is 350,000 lbs. Assembly after delivery is normally 8 – 10 hours requiring 4 Riggers for each of assembly and disassembly. Once assembled, one Rigger using an AWP can attach and adjust the rigging as required. The use of one Rigger and one AWP on each side of the module will increase efficiency. If the spreader bar has to be detached from the crane at the end of each shift as per site requirements, allow 2 Riggers at 1 hour per day for both attaching and detaching it from the crane.
Advantages using QUIKMOD spreader frame include:
- Faster and safer module rigging
- Time to change center of gravity reduced from ½ day to 30 minutes
- Better lift force distribution to the crane hook
- Reduce crane “head room” for rigging
- Minimize rigging inventory compared to traditional rigging setup
- Increase lifts from 1-2 per day to 3-4 per day, thus accelerating the lift schedule
- Optimize crane site utilization and reduce crane cost
Module Fabricators can help reduce time requirements further by 1) ensuring all lifting points are on same elevation plane and 2) using a standard number of pick-points per module (i.e. 4, 6, 8, 10, or 12).
QUIKMOD spreader frame was used to lift modular assembly pipe rack and process skids modules during the construction of a natural gas processing facility built by IAG in Fort Stockton, Texas. Each pipe rack module, up to 16’x16’x90’, 100 tons in weight and process skids module, up to 20’x20’x60’, 30 tons were assembled at the site. QUIKMOD spreader frame reduced rigging and set time from 2 hours to 1 hour.
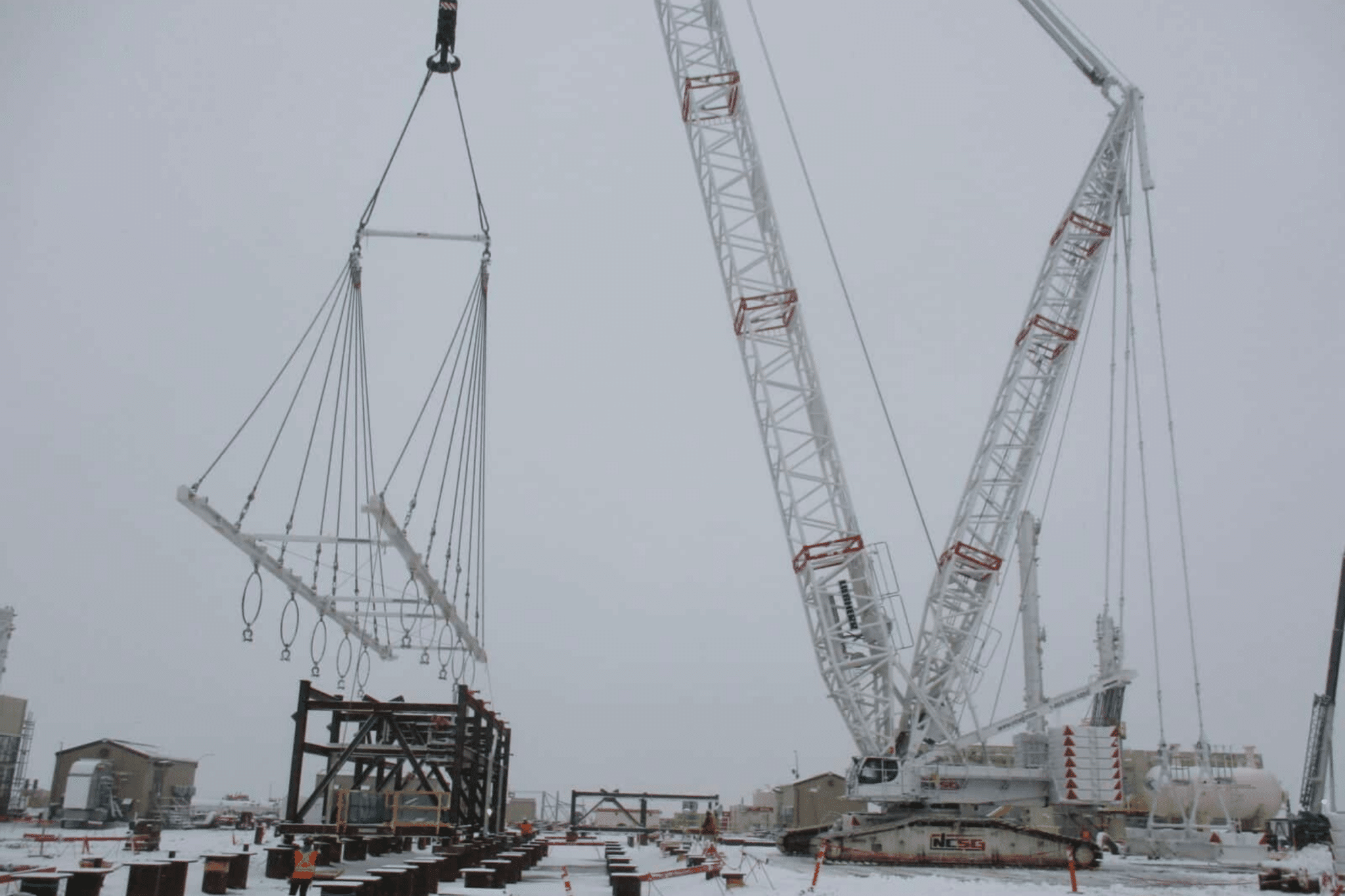